PWM hydrogen current controller explained
The purpose of a PWM controller is to limit/restrict the amps flowing into the HHO generator.
There are two parameters to consider:
– the intended current necessary to operate the generator (consult the amps chart)
– the amperage load the PWM is designed to handle. The load is the unrestricted, free flowing current the generator receives from the battery
A PWM turns the hydrogen generator on and off to achieve an average operational current.
A high output generator is able to consume 100 amps of current. The PWM will do its best to average and limit the current to your set point of 10 amps. It will turn the generator on and off to create the average of 10 amps.
Each PWM controller has a load limitation. If the load specification is less than the load, the controller will be destroyed.
The use of a fuse will NOT protect the PWM. The reaction time of a fuse to current spikes and pulses is much slower. A very fast pulse of 100 amps may not blow a 10 amp fuse because it mostly reacts to the average current. It is these 100 amps pulses that burn PWMs.
1 Understand the maximum current load of the generator
2 Use the least possible amount of electrolyte. Too much electrolyte places an excessive load on the PWM, potentially causing damage.
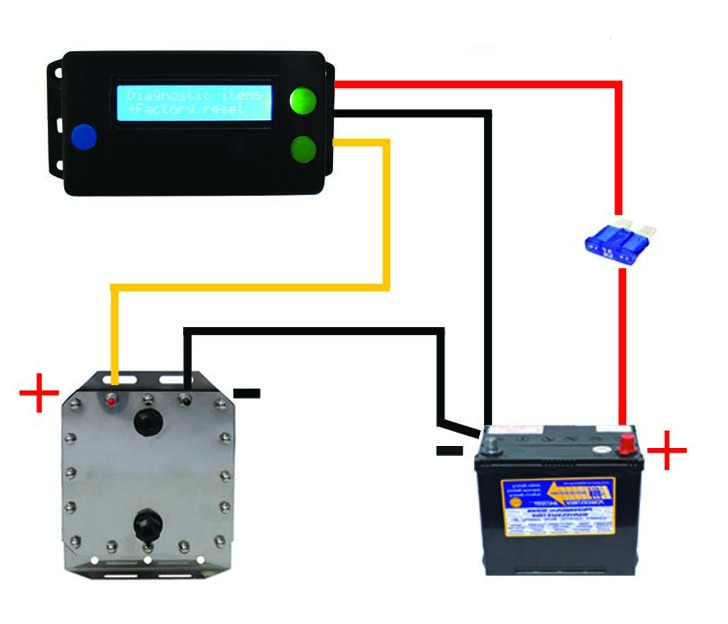
Read more:
Operational temperature of HHO generators
Amount of hydrogen required per size of the engine
How to calculate maximum Hydrogen output
Setup and operation of HHO equipment, safety, compatibility
Results of NASA’ s experiments with hydrogen in internal combustion engines
How to convert engines to use hydrogen as primary fuel
What happens when too much hydrogen is supplied to an engine
Buy current controller
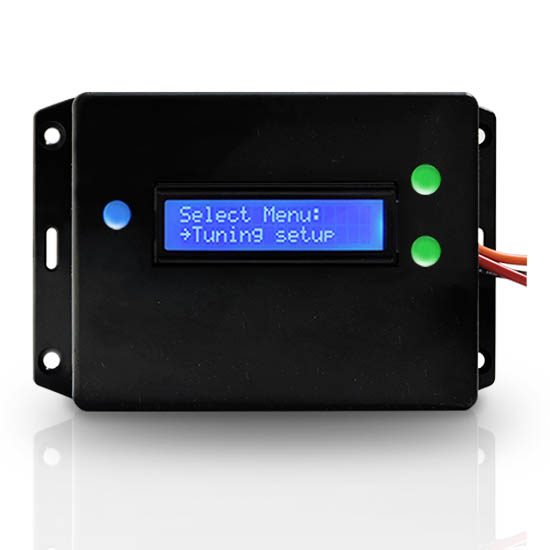
